Where to Find a Backwater Curve Calculations Spreadsheet
To obtain a backwater curve calculations spreadsheet to calculate surface profiles for non uniform open channel flow, click here to visit our spreadsheet store. Obtain a convenient, easy to use backwater curve calculations spreadsheet at a reasonable price. Read on for information about the use of an Excel spreadsheet for non uniform flow open channel surface profile step wise calculations.
Background on Non Uniform and Uniform Open Channel Flow
The diagram at the right illustrates uniform and nonuniform open channel flow. Uniform flow in an open channel consists of a constant volumetric flow of liquid through a reach of channel with a constant bottom slope, surface roughness, and hydraulic radius (that is constant channel size and shape). For those constant channel conditions, the water will flow at a constant depth, called the normal depth, for the particular channel conditions and volumetric flow rate. The diagram shows a reach of uniform open channel flow, followed by a change in bottom slope that causes non-uniform flow, ending with another reach of uniform open channel flow. This article is about means of calculating the surface profile (depth vs distance down the channel) for a reach of non uniform flow.
Classifications of Non Uniform Open Channel Flow for a Backwater Curve Calculations Spreadsheet
Classifications of Non Uniform Open Channel Flow (Mild or Steep Channel Slope)
The diagram above shows the three possible non uniform flow patterns for a mild slope (channel slope less than the critical slope) and the three for a steep slope (channel slope greater than the critical slope). The three mild slope classifications are M1, M2, and M3. The “M” indicates mild slope and the number shows the relationship among depth of flow, y, critical depth, yc, and normal depth, yo , as shown in the diagram. Similarly the three steep slope classifications are S1, S2, and S3, with the numbers having the same meaning. The diagram shows a typical physical situation that will give rise to each of these six types of non uniform open channel flow.
The Energy Equation for a Backwater Curve Calculations Spreadsheet
The energy equation (the first law of thermodynamics applied to a flowing fluid), which has many applications in fluid mechanics, can be used for non uniform open channel flow surface profile stepwise calculations. The diagram below shows the parameters that will be used at each end of a reach of channel with non uniform flow.
A Reach of Open Channel with Non Uniform Flow
The energy equation written across a reach of channel is illustrated graphically in the diagram above. The sum of the three items on the upstream end of the channel reach must equal the sum of the three items on the downstream end of the channel reach, giving the equation:

Where the parameters in the equation are as follows:
- y1 = the upstream depth of flow in ft (m for S.I. units)
- y2 = the downstream depth of flow in ft (m for S.I. units)
- V1 = the upstream average velocity in ft/sec (m/s for S.I. units)
- V2 = the downstream average velocity in ft/sec (m/s for S.I. units)
- g = the acceleration due to gravity = 32.17 ft/sec2 (9.81 m/s2 for S.I. units)
- ΔL = the horizontal length of the channel reach in ft (m for S.I. units)
- So = the bottom slope of the channel, which is dimensionless
- Sf = the slope of the energy grade line (thus head loss is hL = SfΔL)
For specified flow rate, Q, channel bottom slope, So , Manning roughness coefficient, n, and channel width for a rectangular channel, the energy equation can be used to calculate the length, ΔL, for transition from a known upstream depth, y1 , to a selected downstream depth, y2 . This process can be repeated as many times as necessary to determine the total distance to a specified downstream depth.
The energy equation can be rearranged to give the following equation for ΔL:
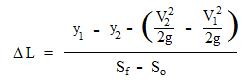
The Manning equation is typically used to calculate the slope of the energy grade line, Sf . Although the Manning equation only applies for uniform flow, the use of mean cross-sectional area and mean hydraulic radius with a relatively small step for the calculation gives a good approximation. The equation for Sf is as follows:
Sf = {Qn/[1.49Am(Rhm2/3)]]}2, where Am is the mean area and Rhmis the mean hydraulic radius between sections 1 and 2. For S.I. units, the 1.49 constant in this equation becomes 1.00.
Screenshot of a Backwater Curve Calculations Spreadsheet
Consider a 20 ft wide rectangular channel with bottom slope equal to 0.0003, carrying 1006 cfs. The normal depth for this flow is 10 ft. An M1 backwater curve is generated due to a downstream obstruction. Calculate the channel length for the transition from a depth of 12 ft to a depth of 12.5 ft in this backwater curve.
Solution: The spreadsheet shown in the screenshot below shows the solution. It actually has the entire M1 curve from a depth of 10 ft to a depth of 16 ft. It shows DL for the transition from 12 ft depth to 12.5 ft depth to be 3853 ft.
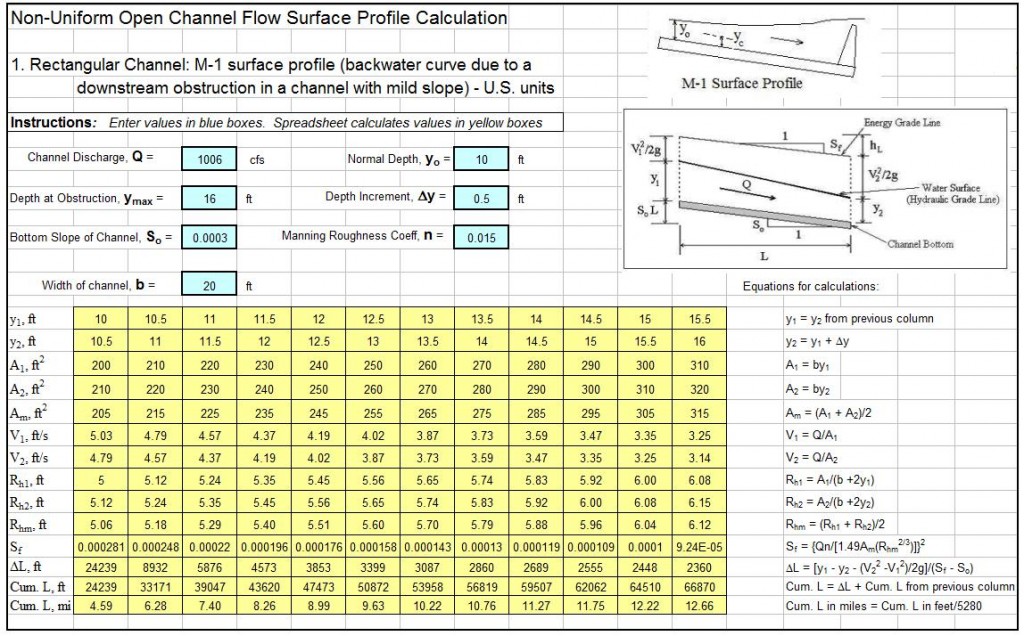
The Excel spreadsheet template shown above can be used to calculate an M1 surface profile for a rectangular channel with specified flow rate, bottom width, bottom slope, and Manning roughness coefficient. Why bother to make these calculations by hand? This backwater curve calculations spreadsheet and others with similar calculations for a trapezoidal channel, and for any of the six mild or steep nonuniform flow surface profiles are available in either U.S. or S.I. units at a very low cost in our spreadsheet store.
References
1. Munson, B. R., Young, D. F., & Okiishi, T. H., Fundamentals of Fluid Mechanics, 4th Ed., New York: John Wiley and Sons, Inc, 2002.
2. Chow, V. T., Open Channel Hydraulics, New York: McGraw-Hill, 1959.
3. Bengtson, Harlan H., Open Channel Flow II – Hydraulic Jumps and Supercritical and Nonuniform Flow – An online, continuing education course for PDH credit.
4. Bengtson, Harlan H., “Non Uniform Flow in Open Channels“, an online blog article